Common Production Processes for Capacitor Applications
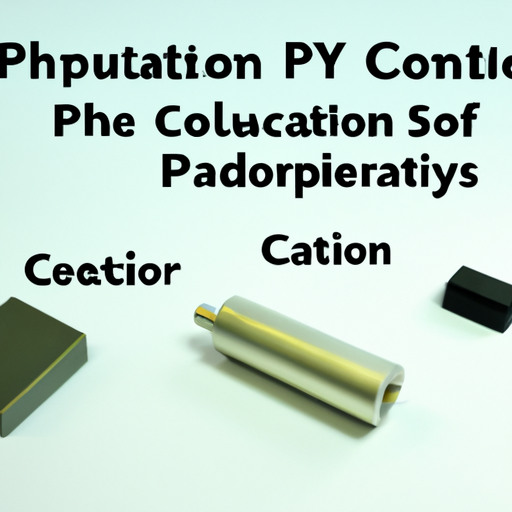
I. Introduction
Capacitors are fundamental components in electronic circuits, serving as energy storage devices that can release energy quickly when needed. They play a crucial role in various applications, from power supply smoothing to signal coupling and decoupling. As technology advances, the demand for capacitors continues to grow, necessitating efficient and innovative production processes. This blog post will explore the common production processes for different types of capacitors, the raw materials used, quality control measures, and emerging trends in capacitor manufacturing.
II. Types of Capacitors
Capacitors come in various types, each suited for specific applications. The most common types include:
A. Ceramic Capacitors
Ceramic capacitors are widely used due to their small size, low cost, and reliability. They are often found in high-frequency applications and are characterized by their dielectric material, which is typically made from ceramic compounds.
B. Electrolytic Capacitors
Electrolytic capacitors are known for their high capacitance values and are commonly used in power supply circuits. They utilize an electrolyte as one of their plates, which allows for a larger surface area and, consequently, higher capacitance.
C. Film Capacitors
Film capacitors use thin plastic films as their dielectric material. They are known for their stability and low loss characteristics, making them suitable for audio and high-frequency applications.
D. Tantalum Capacitors
Tantalum capacitors are known for their high capacitance in a small volume. They are often used in applications where space is limited, such as in mobile devices and computers.
E. Supercapacitors
Supercapacitors, or ultracapacitors, are energy storage devices that bridge the gap between traditional capacitors and batteries. They offer high energy density and rapid charge/discharge capabilities, making them ideal for applications requiring quick bursts of energy.
III. Raw Materials Used in Capacitor Production
The production of capacitors involves various raw materials, primarily dielectric and conductive materials.
A. Dielectric Materials
1. **Ceramic Materials**: Used in ceramic capacitors, these materials provide excellent dielectric properties and stability over a wide temperature range.
2. **Polymer Films**: Employed in film capacitors, polymer films offer flexibility and can be engineered for specific electrical properties.
3. **Electrolytes**: In electrolytic and supercapacitors, electrolytes are crucial for enabling ion movement, which is essential for charge storage.
B. Conductive Materials
1. **Metals**: Aluminum and tantalum are commonly used as conductive materials in electrolytic and tantalum capacitors, respectively. Their high conductivity and ability to form a stable oxide layer make them ideal for capacitor applications.
2. **Conductive Polymers**: These materials are increasingly used in various capacitor types due to their lightweight and flexible properties.
IV. Common Production Processes
The production processes for capacitors vary depending on the type. Below are the common processes for each type of capacitor.
A. Ceramic Capacitor Production
1. **Material Preparation**: The production begins with the preparation of ceramic powders, which are mixed with additives to enhance their dielectric properties.
2. **Dielectric Layer Formation**: The mixed powders are then pressed into thin layers, which are subsequently dried to remove moisture.
3. **Electrode Application**: Conductive electrodes are applied to the dielectric layers, typically using screen printing or sputtering techniques.
4. **Sintering Process**: The assembled layers are sintered at high temperatures to achieve the desired dielectric properties and mechanical strength.
5. **Packaging and Testing**: Finally, the capacitors are packaged, and rigorous testing is conducted to ensure they meet quality standards.
B. Electrolytic Capacitor Production
1. **Anodization of Aluminum**: The production starts with anodizing aluminum foils to create a thin oxide layer, which serves as the dielectric.
2. **Electrolyte Filling**: The anodized aluminum is then filled with an electrolyte, which is essential for the capacitor's operation.
3. **Sealing and Packaging**: After filling, the capacitors are sealed to prevent leakage and packaged for distribution.
4. **Quality Control Measures**: Each capacitor undergoes quality control testing to ensure reliability and performance.
C. Film Capacitor Production
1. **Film Extrusion**: The production begins with the extrusion of polymer films, which are then stretched to enhance their dielectric properties.
2. **Metallization**: A thin layer of metal is deposited onto the film to create the electrodes.
3. **Winding or Stacking**: The metallized film is either wound into a cylindrical shape or stacked in layers, depending on the design.
4. **Encapsulation and Testing**: The final step involves encapsulating the capacitors to protect them from environmental factors and conducting testing to ensure quality.
D. Tantalum Capacitor Production
1. **Tantalum Powder Preparation**: Tantalum powder is prepared and processed into pellets.
2. **Pelleting and Sintering**: The pellets are sintered to form a solid tantalum anode.
3. **Anodization and Electrolyte Application**: The tantalum anode is anodized to create a dielectric layer, followed by the application of an electrolyte.
4. **Final Assembly and Testing**: The capacitors are assembled, tested, and packaged for distribution.
E. Supercapacitor Production
1. **Electrode Preparation**: The production begins with the preparation of electrodes, often made from activated carbon or other high-surface-area materials.
2. **Electrolyte Selection and Application**: An appropriate electrolyte is selected and applied to the electrodes.
3. **Cell Assembly**: The electrodes are assembled into cells, which are then sealed.
4. **Testing and Quality Assurance**: Each supercapacitor undergoes rigorous testing to ensure performance and reliability.
V. Quality Control in Capacitor Production
Quality control is paramount in capacitor production, as even minor defects can lead to failures in electronic devices.
A. Importance of Quality Control
Quality control ensures that capacitors meet the required specifications and performance standards, which is critical for maintaining the reliability of electronic systems.
B. Testing Methods
1. **Electrical Testing**: Capacitors are subjected to electrical tests to measure parameters such as capacitance, equivalent series resistance (ESR), and leakage current.
2. **Environmental Testing**: Capacitors are tested under various environmental conditions, including temperature and humidity, to assess their performance in real-world applications.
3. **Reliability Testing**: Long-term reliability tests are conducted to evaluate the lifespan and durability of capacitors under stress conditions.
VI. Innovations and Trends in Capacitor Manufacturing
The capacitor manufacturing industry is evolving, driven by advancements in materials science and technology.
A. Advances in Materials Science
New materials are being developed to enhance the performance of capacitors, such as high-k dielectrics and conductive polymers, which can improve energy density and efficiency.
B. Automation and Industry 4.0
The integration of automation and smart manufacturing technologies is streamlining production processes, reducing costs, and improving quality control.
C. Environmental Considerations and Sustainability
Manufacturers are increasingly focusing on sustainable practices, such as reducing waste and using eco-friendly materials, to minimize their environmental impact.
VII. Conclusion
In summary, capacitors are essential components in modern electronics, and their production involves a variety of processes tailored to different types. Understanding these processes, the raw materials used, and the importance of quality control is crucial for ensuring the reliability of electronic devices. As the industry continues to innovate, the future of capacitor production looks promising, with advancements in materials and manufacturing technologies paving the way for more efficient and sustainable practices.
VIII. References
1. Academic journals on capacitor technology and materials science.
2. Industry reports on capacitor market trends and innovations.
3. Manufacturer guidelines and specifications for capacitor production processes.
This comprehensive overview of capacitor production processes highlights the complexity and importance of these components in the electronics industry, emphasizing the need for ongoing research and development to meet future demands.
Common Production Processes for Capacitor Applications
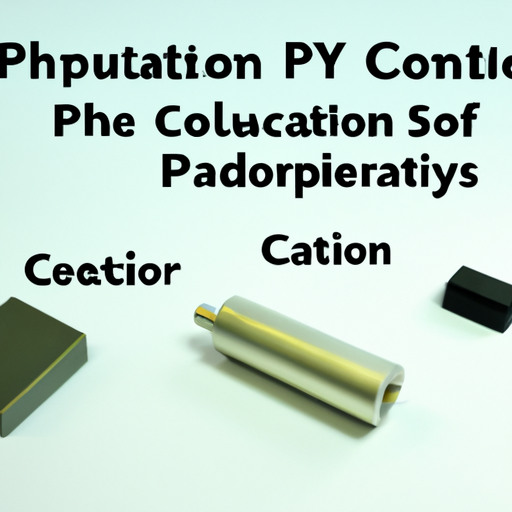
I. Introduction
Capacitors are fundamental components in electronic circuits, serving as energy storage devices that can release energy quickly when needed. They play a crucial role in various applications, from power supply smoothing to signal coupling and decoupling. As technology advances, the demand for capacitors continues to grow, necessitating efficient and innovative production processes. This blog post will explore the common production processes for different types of capacitors, the raw materials used, quality control measures, and emerging trends in capacitor manufacturing.
II. Types of Capacitors
Capacitors come in various types, each suited for specific applications. The most common types include:
A. Ceramic Capacitors
Ceramic capacitors are widely used due to their small size, low cost, and reliability. They are often found in high-frequency applications and are characterized by their dielectric material, which is typically made from ceramic compounds.
B. Electrolytic Capacitors
Electrolytic capacitors are known for their high capacitance values and are commonly used in power supply circuits. They utilize an electrolyte as one of their plates, which allows for a larger surface area and, consequently, higher capacitance.
C. Film Capacitors
Film capacitors use thin plastic films as their dielectric material. They are known for their stability and low loss characteristics, making them suitable for audio and high-frequency applications.
D. Tantalum Capacitors
Tantalum capacitors are known for their high capacitance in a small volume. They are often used in applications where space is limited, such as in mobile devices and computers.
E. Supercapacitors
Supercapacitors, or ultracapacitors, are energy storage devices that bridge the gap between traditional capacitors and batteries. They offer high energy density and rapid charge/discharge capabilities, making them ideal for applications requiring quick bursts of energy.
III. Raw Materials Used in Capacitor Production
The production of capacitors involves various raw materials, primarily dielectric and conductive materials.
A. Dielectric Materials
1. **Ceramic Materials**: Used in ceramic capacitors, these materials provide excellent dielectric properties and stability over a wide temperature range.
2. **Polymer Films**: Employed in film capacitors, polymer films offer flexibility and can be engineered for specific electrical properties.
3. **Electrolytes**: In electrolytic and supercapacitors, electrolytes are crucial for enabling ion movement, which is essential for charge storage.
B. Conductive Materials
1. **Metals**: Aluminum and tantalum are commonly used as conductive materials in electrolytic and tantalum capacitors, respectively. Their high conductivity and ability to form a stable oxide layer make them ideal for capacitor applications.
2. **Conductive Polymers**: These materials are increasingly used in various capacitor types due to their lightweight and flexible properties.
IV. Common Production Processes
The production processes for capacitors vary depending on the type. Below are the common processes for each type of capacitor.
A. Ceramic Capacitor Production
1. **Material Preparation**: The production begins with the preparation of ceramic powders, which are mixed with additives to enhance their dielectric properties.
2. **Dielectric Layer Formation**: The mixed powders are then pressed into thin layers, which are subsequently dried to remove moisture.
3. **Electrode Application**: Conductive electrodes are applied to the dielectric layers, typically using screen printing or sputtering techniques.
4. **Sintering Process**: The assembled layers are sintered at high temperatures to achieve the desired dielectric properties and mechanical strength.
5. **Packaging and Testing**: Finally, the capacitors are packaged, and rigorous testing is conducted to ensure they meet quality standards.
B. Electrolytic Capacitor Production
1. **Anodization of Aluminum**: The production starts with anodizing aluminum foils to create a thin oxide layer, which serves as the dielectric.
2. **Electrolyte Filling**: The anodized aluminum is then filled with an electrolyte, which is essential for the capacitor's operation.
3. **Sealing and Packaging**: After filling, the capacitors are sealed to prevent leakage and packaged for distribution.
4. **Quality Control Measures**: Each capacitor undergoes quality control testing to ensure reliability and performance.
C. Film Capacitor Production
1. **Film Extrusion**: The production begins with the extrusion of polymer films, which are then stretched to enhance their dielectric properties.
2. **Metallization**: A thin layer of metal is deposited onto the film to create the electrodes.
3. **Winding or Stacking**: The metallized film is either wound into a cylindrical shape or stacked in layers, depending on the design.
4. **Encapsulation and Testing**: The final step involves encapsulating the capacitors to protect them from environmental factors and conducting testing to ensure quality.
D. Tantalum Capacitor Production
1. **Tantalum Powder Preparation**: Tantalum powder is prepared and processed into pellets.
2. **Pelleting and Sintering**: The pellets are sintered to form a solid tantalum anode.
3. **Anodization and Electrolyte Application**: The tantalum anode is anodized to create a dielectric layer, followed by the application of an electrolyte.
4. **Final Assembly and Testing**: The capacitors are assembled, tested, and packaged for distribution.
E. Supercapacitor Production
1. **Electrode Preparation**: The production begins with the preparation of electrodes, often made from activated carbon or other high-surface-area materials.
2. **Electrolyte Selection and Application**: An appropriate electrolyte is selected and applied to the electrodes.
3. **Cell Assembly**: The electrodes are assembled into cells, which are then sealed.
4. **Testing and Quality Assurance**: Each supercapacitor undergoes rigorous testing to ensure performance and reliability.
V. Quality Control in Capacitor Production
Quality control is paramount in capacitor production, as even minor defects can lead to failures in electronic devices.
A. Importance of Quality Control
Quality control ensures that capacitors meet the required specifications and performance standards, which is critical for maintaining the reliability of electronic systems.
B. Testing Methods
1. **Electrical Testing**: Capacitors are subjected to electrical tests to measure parameters such as capacitance, equivalent series resistance (ESR), and leakage current.
2. **Environmental Testing**: Capacitors are tested under various environmental conditions, including temperature and humidity, to assess their performance in real-world applications.
3. **Reliability Testing**: Long-term reliability tests are conducted to evaluate the lifespan and durability of capacitors under stress conditions.
VI. Innovations and Trends in Capacitor Manufacturing
The capacitor manufacturing industry is evolving, driven by advancements in materials science and technology.
A. Advances in Materials Science
New materials are being developed to enhance the performance of capacitors, such as high-k dielectrics and conductive polymers, which can improve energy density and efficiency.
B. Automation and Industry 4.0
The integration of automation and smart manufacturing technologies is streamlining production processes, reducing costs, and improving quality control.
C. Environmental Considerations and Sustainability
Manufacturers are increasingly focusing on sustainable practices, such as reducing waste and using eco-friendly materials, to minimize their environmental impact.
VII. Conclusion
In summary, capacitors are essential components in modern electronics, and their production involves a variety of processes tailored to different types. Understanding these processes, the raw materials used, and the importance of quality control is crucial for ensuring the reliability of electronic devices. As the industry continues to innovate, the future of capacitor production looks promising, with advancements in materials and manufacturing technologies paving the way for more efficient and sustainable practices.
VIII. References
1. Academic journals on capacitor technology and materials science.
2. Industry reports on capacitor market trends and innovations.
3. Manufacturer guidelines and specifications for capacitor production processes.
This comprehensive overview of capacitor production processes highlights the complexity and importance of these components in the electronics industry, emphasizing the need for ongoing research and development to meet future demands.