What are the Product Standards for Capacitor Equipment?
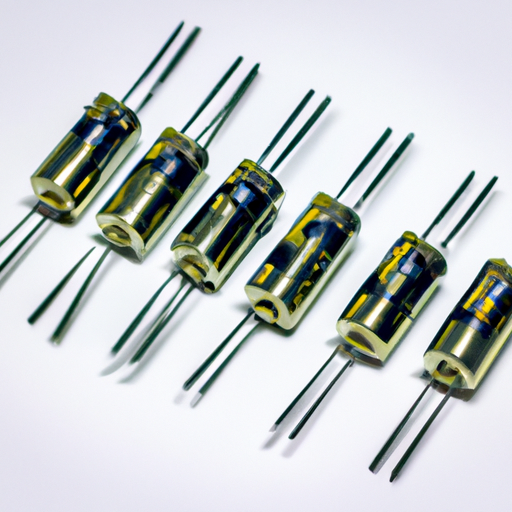
I. Introduction
Capacitors are fundamental components in electrical systems, serving as energy storage devices that can release energy quickly when needed. They play a crucial role in various applications, from smoothing out voltage fluctuations in power supplies to enabling signal processing in electronic circuits. Given their widespread use, the importance of product standards in ensuring the safety, reliability, and performance of capacitor equipment cannot be overstated. This blog post aims to provide a comprehensive overview of the product standards for capacitor equipment, exploring their significance, the organizations involved in setting these standards, and the major standards that govern capacitor manufacturing and testing.
II. Understanding Capacitor Equipment
A. Types of Capacitors
Capacitors come in various types, each designed for specific applications and operating conditions. The most common types include:
1. **Electrolytic Capacitors**: Known for their high capacitance values, these capacitors are polarized and typically used in power supply applications.
2. **Ceramic Capacitors**: These non-polarized capacitors are widely used in high-frequency applications due to their stability and low losses.
3. **Film Capacitors**: Made from plastic films, these capacitors are known for their reliability and are often used in audio and power applications.
4. **Tantalum Capacitors**: These capacitors offer high capacitance in a small package and are commonly used in portable electronics.
B. Applications of Capacitors in Various Industries
Capacitors find applications across multiple industries, including:
1. **Consumer Electronics**: Used in devices like smartphones, televisions, and computers to stabilize power supply and filter signals.
2. **Automotive**: Capacitors are essential in modern vehicles for functions such as energy storage in hybrid systems and noise filtering in electronic control units.
3. **Industrial Machinery**: Employed in motor drives and power factor correction systems to enhance efficiency and performance.
4. **Renewable Energy Systems**: Capacitors play a vital role in energy storage systems and inverters, helping to manage energy flow and improve system stability.
III. Importance of Product Standards
A. Ensuring Safety and Compliance
Product standards are critical in ensuring that capacitor equipment meets safety requirements. They help prevent electrical failures that could lead to hazardous situations, such as fires or equipment damage.
B. Enhancing Product Reliability and Performance
Standards provide guidelines for manufacturing processes, materials, and testing methods, ensuring that capacitors perform reliably under specified conditions. This reliability is essential for maintaining the integrity of electronic systems.
C. Facilitating International Trade and Market Access
Adhering to recognized product standards allows manufacturers to access global markets more easily. Compliance with international standards can simplify the certification process and reduce barriers to trade.
D. Protecting Consumers and Manufacturers
Standards protect consumers by ensuring that products are safe and perform as expected. For manufacturers, compliance with standards can enhance brand reputation and reduce liability risks.
IV. Key Organizations Involved in Setting Standards
Several organizations play a pivotal role in establishing product standards for capacitors:
A. International Electrotechnical Commission (IEC)
The IEC develops international standards for electrical and electronic technologies. Key IEC standards relevant to capacitors include IEC 60384, which covers fixed capacitors for use in electronic equipment.
B. Institute of Electrical and Electronics Engineers (IEEE)
IEEE is a leading organization in the development of standards for electrical and electronic systems. Their standards for capacitors focus on measurement techniques and application guidelines.
C. Underwriters Laboratories (UL)
UL is a global safety certification organization that tests and certifies products for safety and performance. Their UL 810 standard specifically addresses safety criteria for capacitors.
D. Other Relevant Organizations
Other organizations, such as the American National Standards Institute (ANSI) and the International Organization for Standardization (ISO), also contribute to the development of standards that impact capacitor equipment.
V. Major Product Standards for Capacitor Equipment
A. IEC 60384 - Fixed Capacitors for Use in Electronic Equipment
IEC 60384 outlines the requirements for fixed capacitors used in electronic equipment. It covers aspects such as electrical characteristics, testing methods, and safety considerations.
B. IEC 61071 - Capacitors for Power Electronics
This standard focuses on capacitors used in power electronic applications, providing guidelines for their design, testing, and performance.
C. IEEE 18 - Standard for the Measurement of Capacitance
IEEE 18 specifies methods for measuring capacitance, which is crucial for quality assurance and ensuring that capacitors meet their specified values.
D. UL 810 - Standard for Capacitors
UL 810 sets safety and performance criteria for capacitors, ensuring that they can operate safely under specified conditions.
E. Other Relevant Standards
Additional standards, such as RoHS (Restriction of Hazardous Substances) and REACH (Registration, Evaluation, Authorisation, and Restriction of Chemicals), address environmental considerations and the use of hazardous materials in capacitor manufacturing.
VI. Testing and Quality Assurance
A. Importance of Testing in the Manufacturing Process
Testing is a critical component of the manufacturing process for capacitors. It ensures that products meet the required specifications and standards before they reach the market.
B. Common Testing Methods for Capacitors
1. **Capacitance Measurement**: This method verifies that the capacitor's capacitance value meets specifications.
2. **Insulation Resistance Testing**: This test assesses the insulation properties of the capacitor, ensuring it can withstand voltage without leakage.
3. **Dielectric Strength Testing**: This test evaluates the capacitor's ability to withstand high voltages without breaking down.
C. Role of Third-Party Testing Laboratories
Third-party testing laboratories provide independent verification of compliance with standards, enhancing credibility and trust in the product.
VII. Compliance and Certification
A. Process of Obtaining Certifications for Capacitor Equipment
Manufacturers must follow a systematic process to obtain certifications for their capacitor equipment. This typically involves product testing, documentation, and submission to relevant certification bodies.
B. Importance of Maintaining Compliance with Standards
Ongoing compliance with product standards is essential for manufacturers to ensure product safety and performance. Regular audits and testing help maintain this compliance.
C. Consequences of Non-Compliance
Failure to comply with product standards can result in serious consequences, including product recalls, legal liabilities, and damage to brand reputation.
VIII. Future Trends in Capacitor Standards
A. Emerging Technologies and Their Impact on Standards
As technology evolves, new applications for capacitors emerge, necessitating updates to existing standards. For example, advancements in electric vehicles and renewable energy systems may lead to new requirements for capacitor performance.
B. Sustainability and Environmental Considerations
There is a growing emphasis on sustainability in manufacturing processes. Standards are increasingly incorporating environmental considerations, such as the use of recyclable materials and the reduction of hazardous substances.
C. The Role of Digitalization and Smart Technologies
The rise of digitalization and smart technologies is influencing capacitor design and application. Standards will need to adapt to address the challenges and opportunities presented by these advancements.
IX. Conclusion
In conclusion, product standards for capacitor equipment are vital for ensuring safety, reliability, and performance across various applications. Manufacturers and stakeholders must prioritize compliance with these standards to protect consumers and enhance their market presence. As technology continues to evolve, the importance of adapting standards to meet new challenges will only grow, shaping the future of the capacitor industry.
X. References
- International Electrotechnical Commission (IEC) Standards
- Institute of Electrical and Electronics Engineers (IEEE) Standards
- Underwriters Laboratories (UL) Standards
- American National Standards Institute (ANSI)
- International Organization for Standardization (ISO)
- RoHS and REACH Regulations
This blog post provides a comprehensive overview of the product standards for capacitor equipment, highlighting their significance and the organizations involved in their development. By understanding these standards, manufacturers can ensure their products meet the necessary safety and performance criteria, ultimately benefiting consumers and the industry as a whole.
What are the Product Standards for Capacitor Equipment?
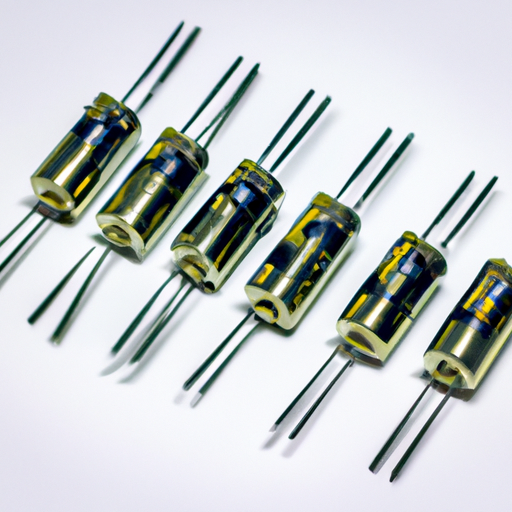
I. Introduction
Capacitors are fundamental components in electrical systems, serving as energy storage devices that can release energy quickly when needed. They play a crucial role in various applications, from smoothing out voltage fluctuations in power supplies to enabling signal processing in electronic circuits. Given their widespread use, the importance of product standards in ensuring the safety, reliability, and performance of capacitor equipment cannot be overstated. This blog post aims to provide a comprehensive overview of the product standards for capacitor equipment, exploring their significance, the organizations involved in setting these standards, and the major standards that govern capacitor manufacturing and testing.
II. Understanding Capacitor Equipment
A. Types of Capacitors
Capacitors come in various types, each designed for specific applications and operating conditions. The most common types include:
1. **Electrolytic Capacitors**: Known for their high capacitance values, these capacitors are polarized and typically used in power supply applications.
2. **Ceramic Capacitors**: These non-polarized capacitors are widely used in high-frequency applications due to their stability and low losses.
3. **Film Capacitors**: Made from plastic films, these capacitors are known for their reliability and are often used in audio and power applications.
4. **Tantalum Capacitors**: These capacitors offer high capacitance in a small package and are commonly used in portable electronics.
B. Applications of Capacitors in Various Industries
Capacitors find applications across multiple industries, including:
1. **Consumer Electronics**: Used in devices like smartphones, televisions, and computers to stabilize power supply and filter signals.
2. **Automotive**: Capacitors are essential in modern vehicles for functions such as energy storage in hybrid systems and noise filtering in electronic control units.
3. **Industrial Machinery**: Employed in motor drives and power factor correction systems to enhance efficiency and performance.
4. **Renewable Energy Systems**: Capacitors play a vital role in energy storage systems and inverters, helping to manage energy flow and improve system stability.
III. Importance of Product Standards
A. Ensuring Safety and Compliance
Product standards are critical in ensuring that capacitor equipment meets safety requirements. They help prevent electrical failures that could lead to hazardous situations, such as fires or equipment damage.
B. Enhancing Product Reliability and Performance
Standards provide guidelines for manufacturing processes, materials, and testing methods, ensuring that capacitors perform reliably under specified conditions. This reliability is essential for maintaining the integrity of electronic systems.
C. Facilitating International Trade and Market Access
Adhering to recognized product standards allows manufacturers to access global markets more easily. Compliance with international standards can simplify the certification process and reduce barriers to trade.
D. Protecting Consumers and Manufacturers
Standards protect consumers by ensuring that products are safe and perform as expected. For manufacturers, compliance with standards can enhance brand reputation and reduce liability risks.
IV. Key Organizations Involved in Setting Standards
Several organizations play a pivotal role in establishing product standards for capacitors:
A. International Electrotechnical Commission (IEC)
The IEC develops international standards for electrical and electronic technologies. Key IEC standards relevant to capacitors include IEC 60384, which covers fixed capacitors for use in electronic equipment.
B. Institute of Electrical and Electronics Engineers (IEEE)
IEEE is a leading organization in the development of standards for electrical and electronic systems. Their standards for capacitors focus on measurement techniques and application guidelines.
C. Underwriters Laboratories (UL)
UL is a global safety certification organization that tests and certifies products for safety and performance. Their UL 810 standard specifically addresses safety criteria for capacitors.
D. Other Relevant Organizations
Other organizations, such as the American National Standards Institute (ANSI) and the International Organization for Standardization (ISO), also contribute to the development of standards that impact capacitor equipment.
V. Major Product Standards for Capacitor Equipment
A. IEC 60384 - Fixed Capacitors for Use in Electronic Equipment
IEC 60384 outlines the requirements for fixed capacitors used in electronic equipment. It covers aspects such as electrical characteristics, testing methods, and safety considerations.
B. IEC 61071 - Capacitors for Power Electronics
This standard focuses on capacitors used in power electronic applications, providing guidelines for their design, testing, and performance.
C. IEEE 18 - Standard for the Measurement of Capacitance
IEEE 18 specifies methods for measuring capacitance, which is crucial for quality assurance and ensuring that capacitors meet their specified values.
D. UL 810 - Standard for Capacitors
UL 810 sets safety and performance criteria for capacitors, ensuring that they can operate safely under specified conditions.
E. Other Relevant Standards
Additional standards, such as RoHS (Restriction of Hazardous Substances) and REACH (Registration, Evaluation, Authorisation, and Restriction of Chemicals), address environmental considerations and the use of hazardous materials in capacitor manufacturing.
VI. Testing and Quality Assurance
A. Importance of Testing in the Manufacturing Process
Testing is a critical component of the manufacturing process for capacitors. It ensures that products meet the required specifications and standards before they reach the market.
B. Common Testing Methods for Capacitors
1. **Capacitance Measurement**: This method verifies that the capacitor's capacitance value meets specifications.
2. **Insulation Resistance Testing**: This test assesses the insulation properties of the capacitor, ensuring it can withstand voltage without leakage.
3. **Dielectric Strength Testing**: This test evaluates the capacitor's ability to withstand high voltages without breaking down.
C. Role of Third-Party Testing Laboratories
Third-party testing laboratories provide independent verification of compliance with standards, enhancing credibility and trust in the product.
VII. Compliance and Certification
A. Process of Obtaining Certifications for Capacitor Equipment
Manufacturers must follow a systematic process to obtain certifications for their capacitor equipment. This typically involves product testing, documentation, and submission to relevant certification bodies.
B. Importance of Maintaining Compliance with Standards
Ongoing compliance with product standards is essential for manufacturers to ensure product safety and performance. Regular audits and testing help maintain this compliance.
C. Consequences of Non-Compliance
Failure to comply with product standards can result in serious consequences, including product recalls, legal liabilities, and damage to brand reputation.
VIII. Future Trends in Capacitor Standards
A. Emerging Technologies and Their Impact on Standards
As technology evolves, new applications for capacitors emerge, necessitating updates to existing standards. For example, advancements in electric vehicles and renewable energy systems may lead to new requirements for capacitor performance.
B. Sustainability and Environmental Considerations
There is a growing emphasis on sustainability in manufacturing processes. Standards are increasingly incorporating environmental considerations, such as the use of recyclable materials and the reduction of hazardous substances.
C. The Role of Digitalization and Smart Technologies
The rise of digitalization and smart technologies is influencing capacitor design and application. Standards will need to adapt to address the challenges and opportunities presented by these advancements.
IX. Conclusion
In conclusion, product standards for capacitor equipment are vital for ensuring safety, reliability, and performance across various applications. Manufacturers and stakeholders must prioritize compliance with these standards to protect consumers and enhance their market presence. As technology continues to evolve, the importance of adapting standards to meet new challenges will only grow, shaping the future of the capacitor industry.
X. References
- International Electrotechnical Commission (IEC) Standards
- Institute of Electrical and Electronics Engineers (IEEE) Standards
- Underwriters Laboratories (UL) Standards
- American National Standards Institute (ANSI)
- International Organization for Standardization (ISO)
- RoHS and REACH Regulations
This blog post provides a comprehensive overview of the product standards for capacitor equipment, highlighting their significance and the organizations involved in their development. By understanding these standards, manufacturers can ensure their products meet the necessary safety and performance criteria, ultimately benefiting consumers and the industry as a whole.