What are the Manufacturing Processes of the Latest Capacitor C?
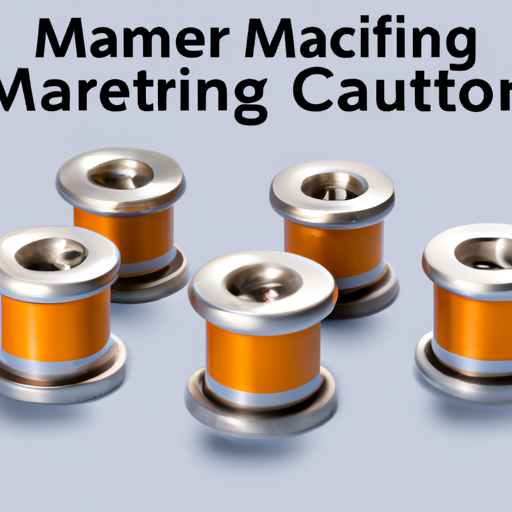
I. Introduction
Capacitors are fundamental components in modern electronics, serving as energy storage devices that can release energy quickly when needed. They play a crucial role in various applications, from power supply circuits to signal processing in communication devices. As technology advances, the demand for more efficient and reliable capacitors has led to the development of the latest capacitor C, which boasts unique features and specifications that cater to the needs of contemporary electronic systems. This blog post will explore the manufacturing processes of capacitor C, shedding light on the materials, techniques, and innovations that define its production.
II. Types of Capacitors
Capacitors come in various types, each designed for specific applications and performance characteristics. The most common types include:
1. **Ceramic Capacitors**: Known for their stability and reliability, ceramic capacitors are widely used in high-frequency applications.
2. **Electrolytic Capacitors**: These capacitors offer high capacitance values and are often used in power supply circuits.
3. **Film Capacitors**: With excellent electrical characteristics, film capacitors are used in audio and power applications.
4. **Tantalum Capacitors**: Known for their compact size and high capacitance, tantalum capacitors are used in space-constrained applications.
The latest capacitor C is a new entrant in this landscape, featuring advanced materials and design that enhance its performance. Its unique specifications make it suitable for a wide range of applications, including renewable energy systems, electric vehicles, and high-frequency communication devices.
III. Raw Materials Used in Capacitor Manufacturing
The manufacturing of capacitor C begins with the selection of high-quality raw materials, which are critical to its performance.
A. Dielectric Materials
The dielectric material is a key component of any capacitor, as it separates the conductive plates and stores electrical energy. For capacitor C, advanced dielectric materials are used, including:
Ceramic Dielectrics: These materials offer high dielectric constants and stability over a wide temperature range.
Polymer Dielectrics: Known for their flexibility and lightweight properties, polymer dielectrics are increasingly used in modern capacitors.
The selection of dielectric materials is based on their electrical properties, thermal stability, and compatibility with other materials used in the capacitor.
B. Conductive Materials
Conductive materials are essential for the capacitor's performance, as they determine the efficiency of energy storage and discharge. Common conductive materials used in capacitor C include:
Aluminum: Often used in electrolytic capacitors for its high conductivity and cost-effectiveness.
Tantalum: Utilized in tantalum capacitors for its excellent conductivity and stability.
The choice of conductive materials directly impacts the capacitor's performance, including its capacitance, voltage rating, and leakage current.
C. Other Materials
In addition to dielectrics and conductors, other materials play a vital role in capacitor manufacturing:
Insulating Materials: These materials prevent electrical leakage and ensure the capacitor operates safely.
Packaging Materials: The packaging protects the capacitor from environmental factors and mechanical stress, ensuring reliability and longevity.
IV. Manufacturing Processes of Capacitor C
The manufacturing of capacitor C involves several intricate processes, each contributing to the final product's quality and performance.
A. Design and Prototyping
The first step in manufacturing capacitor C is the design phase, where engineers consider various factors such as capacitance, voltage rating, and physical dimensions. Advanced simulation and modeling techniques are employed to optimize the design before moving to prototyping.
B. Material Preparation
Once the design is finalized, the next step is material preparation. This involves sourcing high-quality raw materials and conducting quality control checks to ensure they meet the required specifications. Pre-treatment processes, such as cleaning and surface treatment, are performed on dielectric and conductive materials to enhance their performance.
C. Fabrication Techniques
The fabrication of capacitor C involves several key techniques:
1. **Layering and Stacking Processes**:
- **Thin-Film Deposition**: This technique involves depositing thin layers of dielectric material onto conductive substrates, allowing for precise control over thickness and uniformity.
- **Thick-Film Printing**: Used for creating thicker layers of conductive materials, this method is ideal for applications requiring higher capacitance.
2. **Etching and Patterning**: This process involves selectively removing material to create the desired patterns on the capacitor's surface, ensuring optimal performance.
3. **Assembly of Capacitor Components**: After fabrication, the various components of the capacitor are assembled, including the dielectric layers and conductive plates.
D. Electrical Testing and Quality Assurance
Quality assurance is critical in capacitor manufacturing. Various testing methods are employed to assess capacitance, voltage rating, and leakage current. These tests ensure that each capacitor meets the stringent performance standards required for its intended application.
E. Packaging and Final Assembly
The final step in the manufacturing process is packaging. The choice of packaging materials is crucial, as they protect the capacitor from environmental factors and mechanical stress. Proper packaging also ensures the reliability and longevity of the capacitor in its application.
V. Innovations in Capacitor Manufacturing
The capacitor manufacturing industry is witnessing significant innovations that enhance performance and sustainability.
A. Advances in Materials Science
Recent developments in materials science have led to the creation of new dielectric materials that offer improved performance characteristics. Additionally, nanotechnology is being applied to enhance the properties of conductive materials, resulting in capacitors with higher efficiency and lower leakage.
B. Automation and Industry 4.0
The integration of automation and Industry 4.0 technologies is revolutionizing capacitor manufacturing. Automated processes improve efficiency and reduce human error, while data analytics enable manufacturers to monitor quality in real-time, leading to continuous improvement.
C. Environmental Considerations
Sustainability is becoming increasingly important in capacitor manufacturing. Manufacturers are adopting sustainable practices, such as using eco-friendly materials and implementing recycling programs for end-of-life capacitors.
VI. Challenges in Capacitor Manufacturing
Despite the advancements in capacitor manufacturing, several challenges persist:
A. Supply Chain Issues
Global supply chain disruptions can impact the availability of raw materials, leading to delays in production and increased costs.
B. Cost Management
Balancing the cost of high-quality materials with competitive pricing remains a challenge for manufacturers.
C. Meeting Regulatory Standards
Compliance with regulatory standards is essential, but it can also add complexity to the manufacturing process.
D. Competition and Market Dynamics
The capacitor market is highly competitive, with constant pressure to innovate and reduce costs.
VII. Future Trends in Capacitor Technology
Looking ahead, several trends are expected to shape the future of capacitor technology:
A. Predictions for the Evolution of Capacitor C
As technology continues to advance, capacitor C is likely to evolve, incorporating new materials and designs that enhance its performance and efficiency.
B. Potential Applications in Emerging Technologies
Capacitor C is poised to play a significant role in emerging technologies, such as electric vehicles, renewable energy systems, and advanced communication networks.
C. Research and Development Directions
Ongoing research and development efforts will focus on improving capacitor performance, reducing costs, and enhancing sustainability.
VIII. Conclusion
In conclusion, capacitor C represents a significant advancement in capacitor technology, driven by innovative manufacturing processes and materials. Understanding these processes—from raw material selection to final assembly—provides valuable insights into the complexities of capacitor production. As the demand for high-performance capacitors continues to grow, the industry must adapt to meet the challenges and seize the opportunities presented by emerging technologies. The future of capacitor technology is bright, with exciting developments on the horizon that promise to enhance the performance and reliability of electronic devices.
IX. References
- Academic journals on capacitor technology and materials science.
- Industry reports detailing trends and innovations in capacitor manufacturing.
- Manufacturer specifications and white papers on the latest capacitor C.
This comprehensive exploration of the manufacturing processes of the latest capacitor C highlights the intricate steps involved in producing a critical component of modern electronics, emphasizing the importance of innovation and quality in the industry.
What are the Manufacturing Processes of the Latest Capacitor C?
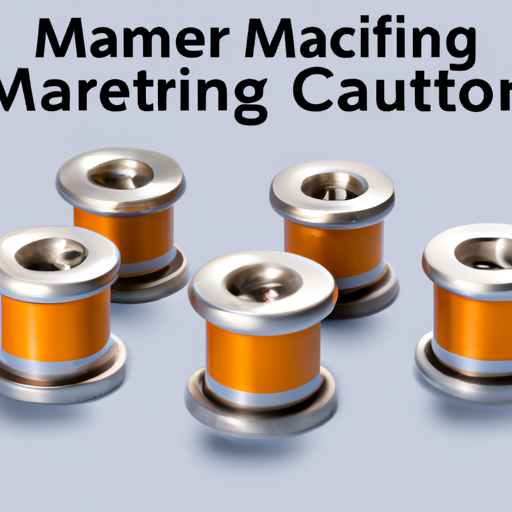
I. Introduction
Capacitors are fundamental components in modern electronics, serving as energy storage devices that can release energy quickly when needed. They play a crucial role in various applications, from power supply circuits to signal processing in communication devices. As technology advances, the demand for more efficient and reliable capacitors has led to the development of the latest capacitor C, which boasts unique features and specifications that cater to the needs of contemporary electronic systems. This blog post will explore the manufacturing processes of capacitor C, shedding light on the materials, techniques, and innovations that define its production.
II. Types of Capacitors
Capacitors come in various types, each designed for specific applications and performance characteristics. The most common types include:
1. **Ceramic Capacitors**: Known for their stability and reliability, ceramic capacitors are widely used in high-frequency applications.
2. **Electrolytic Capacitors**: These capacitors offer high capacitance values and are often used in power supply circuits.
3. **Film Capacitors**: With excellent electrical characteristics, film capacitors are used in audio and power applications.
4. **Tantalum Capacitors**: Known for their compact size and high capacitance, tantalum capacitors are used in space-constrained applications.
The latest capacitor C is a new entrant in this landscape, featuring advanced materials and design that enhance its performance. Its unique specifications make it suitable for a wide range of applications, including renewable energy systems, electric vehicles, and high-frequency communication devices.
III. Raw Materials Used in Capacitor Manufacturing
The manufacturing of capacitor C begins with the selection of high-quality raw materials, which are critical to its performance.
A. Dielectric Materials
The dielectric material is a key component of any capacitor, as it separates the conductive plates and stores electrical energy. For capacitor C, advanced dielectric materials are used, including:
Ceramic Dielectrics: These materials offer high dielectric constants and stability over a wide temperature range.
Polymer Dielectrics: Known for their flexibility and lightweight properties, polymer dielectrics are increasingly used in modern capacitors.
The selection of dielectric materials is based on their electrical properties, thermal stability, and compatibility with other materials used in the capacitor.
B. Conductive Materials
Conductive materials are essential for the capacitor's performance, as they determine the efficiency of energy storage and discharge. Common conductive materials used in capacitor C include:
Aluminum: Often used in electrolytic capacitors for its high conductivity and cost-effectiveness.
Tantalum: Utilized in tantalum capacitors for its excellent conductivity and stability.
The choice of conductive materials directly impacts the capacitor's performance, including its capacitance, voltage rating, and leakage current.
C. Other Materials
In addition to dielectrics and conductors, other materials play a vital role in capacitor manufacturing:
Insulating Materials: These materials prevent electrical leakage and ensure the capacitor operates safely.
Packaging Materials: The packaging protects the capacitor from environmental factors and mechanical stress, ensuring reliability and longevity.
IV. Manufacturing Processes of Capacitor C
The manufacturing of capacitor C involves several intricate processes, each contributing to the final product's quality and performance.
A. Design and Prototyping
The first step in manufacturing capacitor C is the design phase, where engineers consider various factors such as capacitance, voltage rating, and physical dimensions. Advanced simulation and modeling techniques are employed to optimize the design before moving to prototyping.
B. Material Preparation
Once the design is finalized, the next step is material preparation. This involves sourcing high-quality raw materials and conducting quality control checks to ensure they meet the required specifications. Pre-treatment processes, such as cleaning and surface treatment, are performed on dielectric and conductive materials to enhance their performance.
C. Fabrication Techniques
The fabrication of capacitor C involves several key techniques:
1. **Layering and Stacking Processes**:
- **Thin-Film Deposition**: This technique involves depositing thin layers of dielectric material onto conductive substrates, allowing for precise control over thickness and uniformity.
- **Thick-Film Printing**: Used for creating thicker layers of conductive materials, this method is ideal for applications requiring higher capacitance.
2. **Etching and Patterning**: This process involves selectively removing material to create the desired patterns on the capacitor's surface, ensuring optimal performance.
3. **Assembly of Capacitor Components**: After fabrication, the various components of the capacitor are assembled, including the dielectric layers and conductive plates.
D. Electrical Testing and Quality Assurance
Quality assurance is critical in capacitor manufacturing. Various testing methods are employed to assess capacitance, voltage rating, and leakage current. These tests ensure that each capacitor meets the stringent performance standards required for its intended application.
E. Packaging and Final Assembly
The final step in the manufacturing process is packaging. The choice of packaging materials is crucial, as they protect the capacitor from environmental factors and mechanical stress. Proper packaging also ensures the reliability and longevity of the capacitor in its application.
V. Innovations in Capacitor Manufacturing
The capacitor manufacturing industry is witnessing significant innovations that enhance performance and sustainability.
A. Advances in Materials Science
Recent developments in materials science have led to the creation of new dielectric materials that offer improved performance characteristics. Additionally, nanotechnology is being applied to enhance the properties of conductive materials, resulting in capacitors with higher efficiency and lower leakage.
B. Automation and Industry 4.0
The integration of automation and Industry 4.0 technologies is revolutionizing capacitor manufacturing. Automated processes improve efficiency and reduce human error, while data analytics enable manufacturers to monitor quality in real-time, leading to continuous improvement.
C. Environmental Considerations
Sustainability is becoming increasingly important in capacitor manufacturing. Manufacturers are adopting sustainable practices, such as using eco-friendly materials and implementing recycling programs for end-of-life capacitors.
VI. Challenges in Capacitor Manufacturing
Despite the advancements in capacitor manufacturing, several challenges persist:
A. Supply Chain Issues
Global supply chain disruptions can impact the availability of raw materials, leading to delays in production and increased costs.
B. Cost Management
Balancing the cost of high-quality materials with competitive pricing remains a challenge for manufacturers.
C. Meeting Regulatory Standards
Compliance with regulatory standards is essential, but it can also add complexity to the manufacturing process.
D. Competition and Market Dynamics
The capacitor market is highly competitive, with constant pressure to innovate and reduce costs.
VII. Future Trends in Capacitor Technology
Looking ahead, several trends are expected to shape the future of capacitor technology:
A. Predictions for the Evolution of Capacitor C
As technology continues to advance, capacitor C is likely to evolve, incorporating new materials and designs that enhance its performance and efficiency.
B. Potential Applications in Emerging Technologies
Capacitor C is poised to play a significant role in emerging technologies, such as electric vehicles, renewable energy systems, and advanced communication networks.
C. Research and Development Directions
Ongoing research and development efforts will focus on improving capacitor performance, reducing costs, and enhancing sustainability.
VIII. Conclusion
In conclusion, capacitor C represents a significant advancement in capacitor technology, driven by innovative manufacturing processes and materials. Understanding these processes—from raw material selection to final assembly—provides valuable insights into the complexities of capacitor production. As the demand for high-performance capacitors continues to grow, the industry must adapt to meet the challenges and seize the opportunities presented by emerging technologies. The future of capacitor technology is bright, with exciting developments on the horizon that promise to enhance the performance and reliability of electronic devices.
IX. References
- Academic journals on capacitor technology and materials science.
- Industry reports detailing trends and innovations in capacitor manufacturing.
- Manufacturer specifications and white papers on the latest capacitor C.
This comprehensive exploration of the manufacturing processes of the latest capacitor C highlights the intricate steps involved in producing a critical component of modern electronics, emphasizing the importance of innovation and quality in the industry.